Reliable Detection of Bottles Using Ultrasonic Sensors on Filling Production Lines
- Share
- publisher
- Zoe
- Issue Time
- Oct 26,2024
Summary
In highly automated industries such as beverages, pharmaceuticals, and cosmetics, the efficiency and accuracy of filling production lines are crucial. Ultrasonic sensors play a key role in this process.
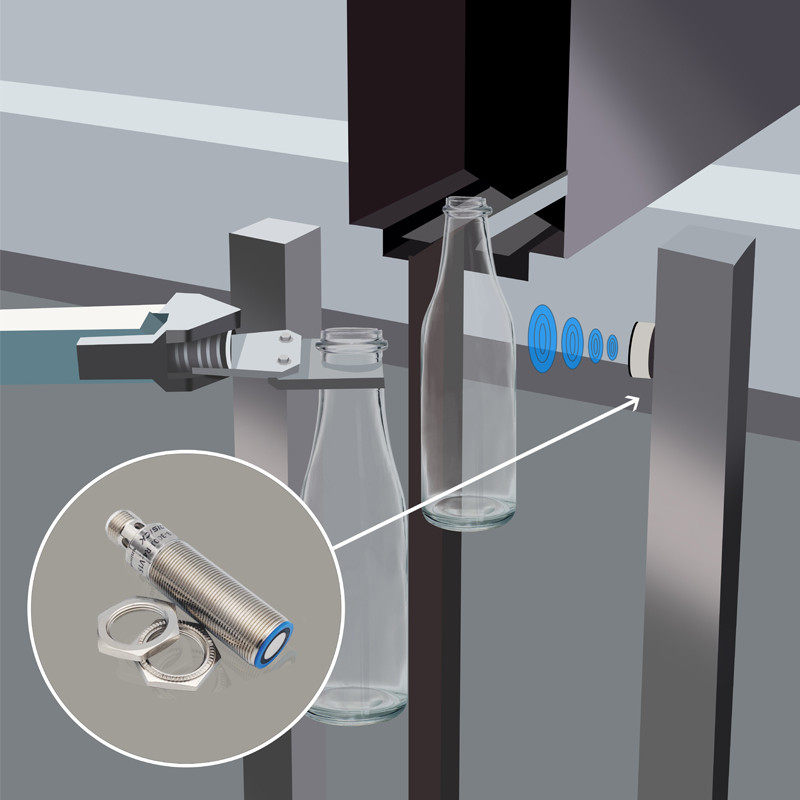
Reliable Detection of Bottles Using Ultrasonic Sensors on Filling Production Lines
In highly automated industries such as beverages, pharmaceuticals, and cosmetics, the efficiency and accuracy of filling production lines are crucial. Ultrasonic sensors play a key role in this process.
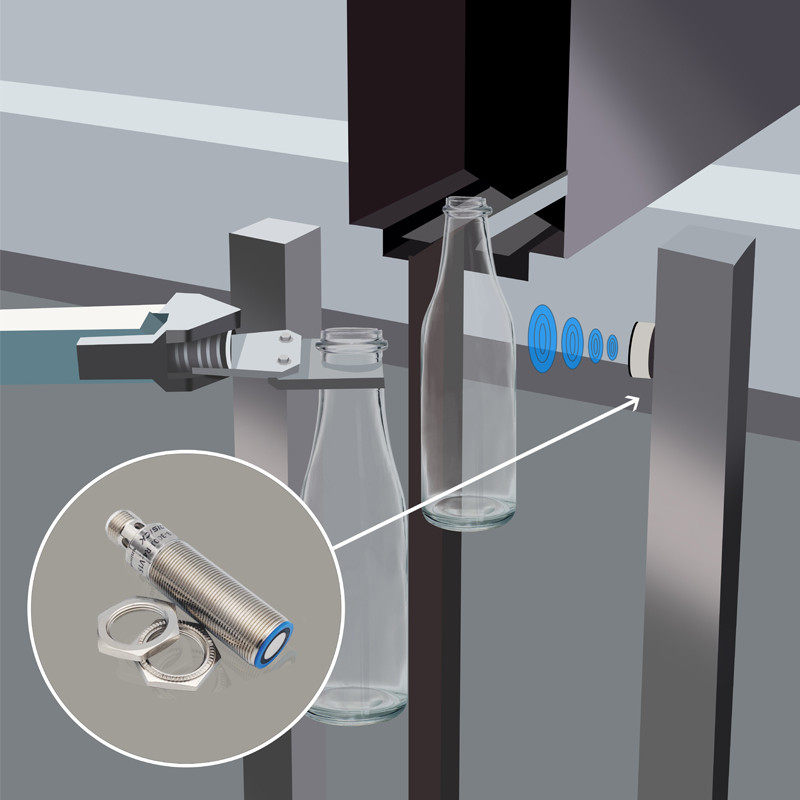
Requirements:
During the material transport phase of the filling production line, ensuring a continuous supply of materials is essential:
◾ Material Entry: Sensors are used to detect the presence and quantity of materials before they enter the filling line, ensuring smooth material supply. Given that bottles can be made from various materials (such as glass, plastic, or ceramic) and come in different colors and transparencies, sensors must operate reliably under these conditions. Additionally, they need to be installed in limited spaces and prevent mutual interference.
◾ Counting Area: At the finished product output line, ultrasonic sensors are employed to count the number of products for inventory management and production statistics.
Solution:
We recommend the CSB18 series ultrasonic sensors, which utilize sound wave detection rather than optical principles, allowing the sound beam to cover a wide area of the container surface. This feature ensures accurate detection even with different contours and position deviations, unaffected by the color and texture of the container's surface. The CSB18 series is particularly suitable for stable detection of uneven surfaces, liquids, transparent objects, and in dirty environments, applicable to both stationary and moving objects.
Technical Features of the CSB18 Series:
✅ Measuring Range: 30 mm to 300 mm, 50 mm to 500 mm, 60 mm to 1000 mm
✅ Small Blind Zones: Options for 30 mm, 50 mm, or 60 mm,✅ Output Types: Optional switch output, IO-Link output, analog output, digital output
✅ Operating Temperature: -25°C to +70°C
✅ Degree of Protection: IP67, ensuring stable operation under various environmental conditions
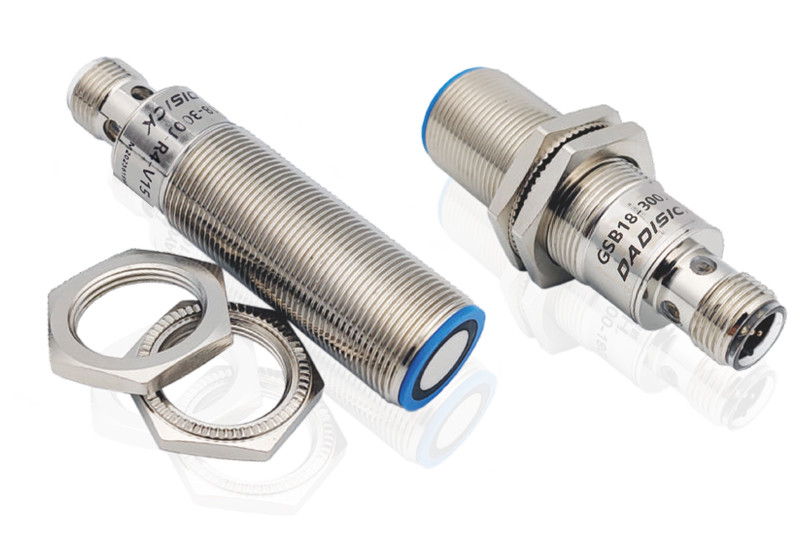
The Advantages of CSB18 Series Ultrasonic Sensor
When multiple ultrasonic sensors are installed closely together, the unique synchronization feature effectively controls multiple sensors to measure simultaneously without interference. The compact design of the CSB18 series provides significant flexibility during installation. Additionally, the series includes built-in temperature compensation to ensure measurement accuracy and supports distance learning functionality via a gray wire.
Product Highlights
◾ Reliable detection of irregular shapes
◾ Unaffected by optical properties and surface conditions
◾ Space-saving design, suitable for installation in narrow spaces
◾ Synchronization feature allows for parallel operation of multiple sensors
◾ IO-Link enables easy debugging
Recommended Ultrasonic Sensors
Replacement for | BALLUFF S-BUS Series Ultrasonic Sensors | CONTRINEX M18 Ultrasonic Sensors | DATASENSING UK1 M18, UK6 M18, US18-PA/PR Series | HTM SENSORS M18U Series Ultrasonic Sensors | IFM UG M18 Ultrasonic Sensors | IPF ELECTRONIC M18 Ultrasonic Sensors for Distance Measurement | Leuze HTU218, HTU318, RKU318, HTU418B Ultrasonic Sensors | PEPPERL+FUCHS 18GM, 18GS Series Ultrasonic Sensors | Wenglor U18T, UMD Series Ultrasonic Distance Sensors | BANNER S18U Series Barrel Ultrasonic Sensors | Rockwell Automation M18 Ultrasonic Sensors
FAQs About Ultrasonic Sensors
What is IO-Link?
IO-Link is an intelligent communication technology that serves as an internationally standardized, vendor-neutral open interface, forming an essential part of DADISICK® solutions. It is standardized according to IEC 61131-9 and is compatible with any fieldbus system on the market. IO-Link sensors can be configured via the control system, simplifying the debugging process and allowing for quick adjustments without increasing downtime.
What are the differences between ultrasonic sensors and optical sensors?
The primary difference between ultrasonic sensors and optical sensors lies in their working principles and application scenarios. Ultrasonic sensors use sound waves for measurement, providing stable detection under various surface conditions (such as liquids, transparent objects, and irregular shapes) and are unaffected by lighting conditions. In contrast, optical sensors rely on light signals and may be interfered with by highly reflective surfaces or environmental conditions like dust or fog. Therefore, ultrasonic sensors are more advantageous in complex and variable environments.
What are the common characteristics of ultrasonic sensors?
1. Non-contact measurement: They can detect objects without physical contact, reducing the risk of wear and damage.
2. Wide measurement range: They can be used to detect objects of different sizes and materials, adapting to various application scenarios.
3. Strong environmental adaptability: They can operate stably in conditions such as humidity, dust, or low light.
4. Multiple output options: They support various output types (such as switch output, analog output, and IO-Link), facilitating integration with different control systems.
Disclaimer: The brands and specifications shown on this page are for product comparison and selection purposes only. Our ultrasonic sensors are manufactured by DADISICK and are not official products of the listed brands. DADISICK offers replacements compatible with these brands' products. We do not own the rights to any of the mentioned brands. If you need to purchase official brand products, please contact the brand official representative.