Application of Ultrasonic Sensors in Vibrating Screw Conveyors: Monitoring Bulk Material Loading Status
- Share
- publisher
- Zoe
- Issue Time
- Oct 23,2024
Summary
In automated production lines, maintaining optimal efficiency and accuracy of these vibrating screw conveyors is essential for overall production performance. Integrating ultrasonic sensors enhances this process by monitoring material levels in real time, preventing empty operation, and enabling the conveyor to start or stop automatically based on material availability. This not only improves energy efficiency but also reduces equipment wear and ensures continuous, smooth production.
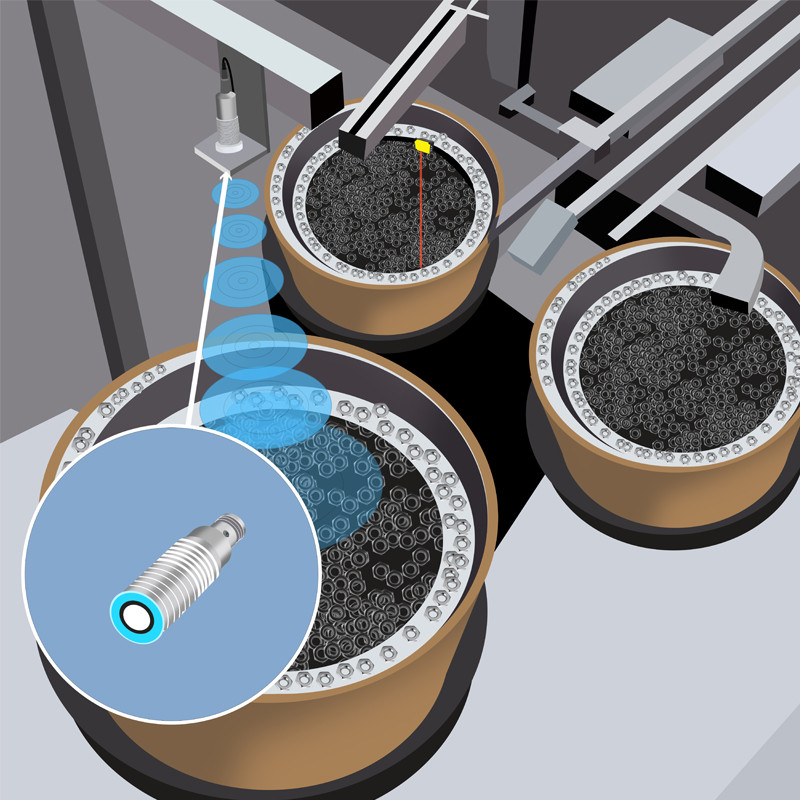
Application of Ultrasonic Sensors in Vibrating Screw Conveyors: Monitoring Bulk Material Loading Status
Vibrating screw conveyors are efficient material handling devices primarily used to sort and precisely place small bulk materials (such as granules, powders, and small parts) into predetermined positions for subsequent automated processing. In automated production lines, the efficiency and accuracy of the conveyor are crucial to overall production performance.
Necessity of Installing Ultrasonic Sensors
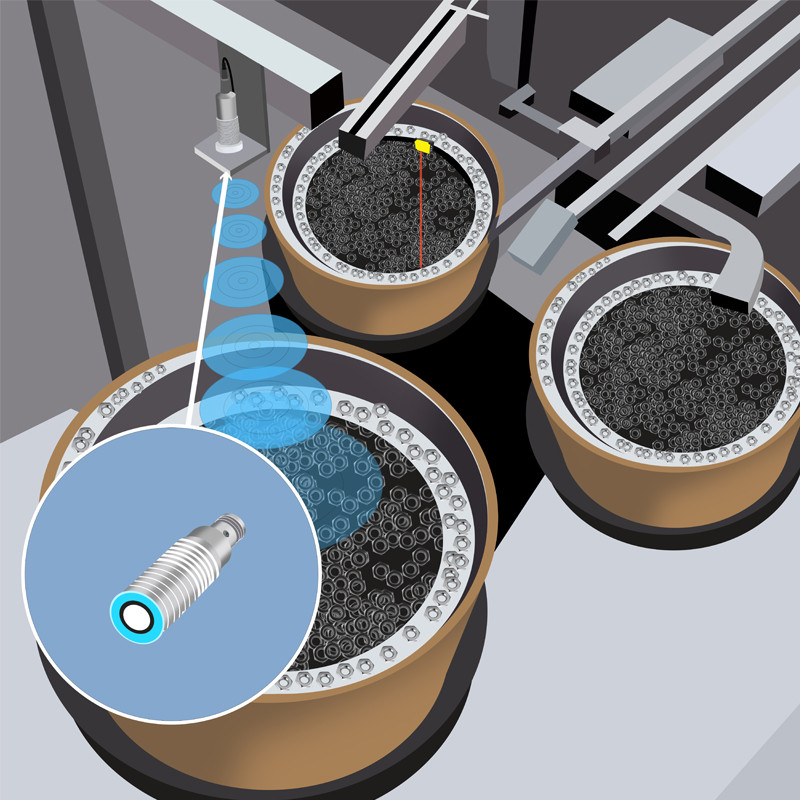
Necessity of Installing Ultrasonic Sensors
To ensure that the screw conveyor and its connected linear conveyor do not run empty when material is missing, the system must be capable of real-time monitoring of material position and loading status. This not only prevents energy waste but also reduces machine wear and extends equipment lifespan.
Function of Ultrasonic Sensors
The CSB18 ultrasonic level sensor plays a critical role in this application. This sensor accurately detects the loading level of materials within the screw conveyor. When the material reaches a preset loading amount, the sensor sends a signal to the control system, indicating whether to continue running the screw conveyor or to pause its operation.
Models
|
CSB18-300 |
CSB18-500
|
CSB18-1000
|
Detection range | 30-300 mm | 50-500 mm | 60-1000 mm |
Blind zone
|
0-30 mm |
0-50 mm
|
0-60 mm
|
Resolution
|
0.1 mm |
0.15 mm
|
0.17 mm
|
Response time | 22 ms | 32 ms | 52 ms |
Switching hysteresis | 2 mm | 2 mm | 2 mm |
Switching frequency | 45 Hz | 31 Hz | 19 Hz |
Repeatability: ±0.15% of full-scale value | |||
Absolute accuracy: ±1 % (built-in temperature drift compensation) | |||
Input type: With synchronization and learning function | |||
Output type: Switch output; IO-Link output; Analog output; Digital output RS485 | |||
Material: Copper nickel plating , plastic fittings , glass filled epoxy resin | |||
Connection type: 5-pin M12 connector | |||
Protection Class: IP67 | |||
Ambient temperature: -25°C~+70°C (248~343K) |
CSB18 Series Ultrasonic Sensor Replacement Options
The CSB18 Series Ultrasonic Sensors, offering various output types including switching output, IO-Link, analog output, and digital output, can serve as a replacement for the following series:
▪️ BALLUFF BUS007F, BUS007K ultrasonic sensors
▪️ BALLUFF BUS007F, BUS007K ultrasonic sensors
▪️ CONTRINEX M18 ultrasonic sensors
▪️ DATASENSING UK1 M18, UK6 M18, US18-PA/PR series
▪️ HTM SENSORS M18U series ultrasonic sensors
▪️ IFM UG M18 ultrasonic sensors
▪️ IPF ELECTRONIC M18 ultrasonic sensors for distance measurement
▪️ Leuze HTU218, HTU318, RKU318, HTU418B ultrasonic sensors
▪️ PEPPERL+FUCHS 18GM, 18GS series ultrasonic sensors
▪️ wenglor U18T, UMD series ultrasonic distance sensors
▪️ BANNER S18U series barrel ultrasonic sensors
▪️ Rockwell Automation M18 ultrasonic sensors
Main Advantages of Ultrasonic Sensors
▪️ Energy Savings: By monitoring material loading status in real-time, the ultrasonic sensor ensures that the screw conveyor operates only when necessary, thereby reducing energy consumption.
▪️ Increased Efficiency: The automated start-stop function minimizes production delays caused by waiting for materials, enhancing overall production line efficiency.
▪️ Reduced Machine Wear: Avoiding idle running in the absence of materials helps reduce wear on mechanical components, lowering maintenance costs.
▪️ Real-time Monitoring: Continuous feedback on material loading status allows operators to adjust production strategies promptly.
The integration of ultrasonic level sensors enables vibratory bowl feeders to automatically start and stop based on real-time material loading conditions. This optimization not only enhances energy use but also improves operational efficiency and reliability. Through this intelligent monitoring, enterprises can achieve more refined production management, lower costs, and improve competitiveness.
Recommended Ultrasonic Sensors
FAQs About Ultrasonic Sensors
How do ultrasonic sensors work?
Ultrasonic sensors emit high-frequency sound waves (usually 23-40 kHz). When these waves hit an object, they bounce back to the sensor. The sensor calculates the time it takes for the sound to return and, using the speed of sound, determines the distance to the object—similar to how bats use echolocation.
What factors can affect ultrasonic sensors?
Ultrasonic sensors can be influenced by temperature changes, which affect the speed of sound and may result in inaccurate distance readings. Air currents from fans or pneumatic devices can also deflect the sound waves, causing the sensor to misinterpret the object's position.
What are common applications for ultrasonic sensors?
Ultrasonic sensors are used in industrial automation for tasks like robot navigation, object detection, and measurement. In smart homes, they are used for human detection, gesture control, and indoor positioning. They are also common in security systems for intrusion detection and tracking, and in vehicles for tasks like automatic parking and obstacle avoidance.
Disclaimer: The brands and specifications shown on this page are for product comparison and selection purposes only. Our ultrasonic sensors are manufactured by DADISICK and are not official products of the listed brands. DADISICK offers replacements compatible with these brands' products. We do not own the rights to any of the mentioned brands. If you need to purchase official brand products, please contact the brand official representative.